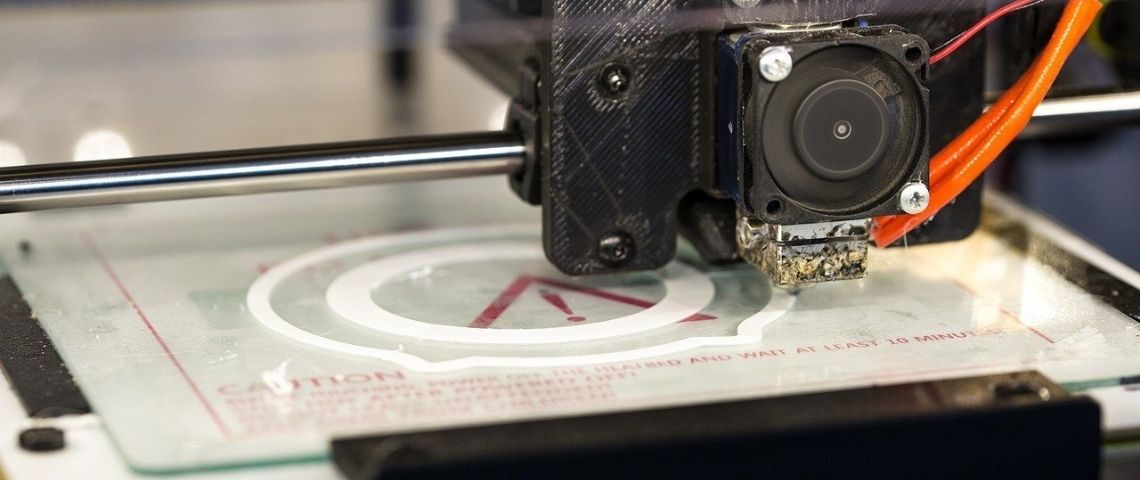
L’un des faits majeurs ayant retenu l’attention des observateurs, c’est l’adaptation de l’industrie 3D dans la recherche des solutions permettant de freiner la propagation de la pandémie de Covid-19. De nombreux produits innovants ont ainsi pu être créés par les entreprises. Cet article passe en revue les applications qui ont le plus impacté le combat mené contre le coronavirus.
La mise à disposition d’équipements de protection respiratoire
Le premier respirateur, fruit de l’impression 3D, a été mis à la disposition des hôpitaux espagnols à la mi-mars 2020. Un consortium de plusieurs entreprises est à la base de ce projet. Il s’agit entre autres de SEAT, de HP, du Consorci de la Zona France (CZFB), du Consorci sanitari de Terrassa (CST), de Leitat et enfin de l’hôpital Tauli à Sabadell.
La raison d’être de cette innovation était d’apporter un soutien aux hôpitaux et aux unités de soins intensifs. La création de ces respirateurs a en effet facilité la prise en charge des malades qui présentaient des formes graves de coronavirus. Le prototypage a été très rapide grâce à l’usage des imprimantes 3D et à une parfaite collaboration entre les différentes parties prenantes du projet.
L’Italie est parmi les pays européens ayant payé un lourd tribut à la pandémie du Covid-19. Comme dans plusieurs autres pays d’Europe, le personnel médical a été mis à rude épreuve. Pénurie d’équipements médicaux, insuffisance de matériel de protection individuelle, hôpitaux débordés, personnels soignants en sous-effectifs, il y avait de nombreux défis à relever.
La création des valves de respiration pour aider les hôpitaux répond à ce besoin. Cette innovation a vu le jour grâce à l’expertise de Isinnova, une entreprise italienne. Le centre hospitalier de Chiari a été le premier à recevoir ces équipements. La fourniture desdites valves en quantité nécessaire par Isinnova a été rendue possible grâce à la fabrication additive.
Impression d’écouvillons et stérilisateurs d’air
Les écouvillons ont l’aspect de cotons-tiges. Leur utilité apparaît au moment de faire des prélèvements nasaux pour la réalisation des tests PCR. Au milieu du printemps 2020, en plein dans la première vague de l’épidémie de Covid-19, un grand besoin en écouvillons s’est fait sentir afin de tester la population pour mieux la protéger.
Face à la forte demande en écouvillons, Formlabs et Carbon se sont lancées dans l’impression de la résine utilisée pour les créer. Très vite, leur capacité de production a atteint un volume journalier estimé à 150 000 écouvillons. Cette innovation a permis d’améliorer la capacité de testing et la prise en charge des malades.
Stérilisation de l’air intérieur et élimination des bactéries et des microorganismes qui s’y trouvent, c’est tout le sens de la mise en place de l’AMS mini. Ce dispositif qui agit comme un stérilisateur a été développé par FICEP S3, une entreprise espagnole. La technologie HP Multi Jet Fusion associée à un nylon de type (PA 12) a servi de socle à cette innovation.
L’appareil assure la purification de l’air grâce aux rayons lumineux ultraviolets. Le système utilisé obéit à un cycle qui force l’air à rester coincé à l’intérieur de l’appareil pour être purifié. La complexité de sa structure fait de l’impression 3D, la seule méthode capable de produire cet appareil. Grâce à son aspect compact, son utilisation est rendue facile dans de nombreux espaces de travail : hôtels, usines, bureaux, laboratoires, hôpitaux, etc.
La fabrication du matériel d’isolement
L’une des premières applications permettant de lutter contre la pandémie a été créée par Winsun, une entreprise chinoise, à la fin du mois de février 2020. L’objet en question est une chambre destinée à isoler les malades ou les personnes présentant les symptômes du Covid-19. La conception des chambres d’isolation s’est faite en extrudant du béton à l’aide d’une imprimante 3D.
Chaque chambre était bâtie sur 10 m2 de surface et mesurait 2,8 m de haut. L’impact de cette application dans la réduction du nombre des contaminations a été salué par toute la communauté scientifique. Ces lieux d’isolement ont prouvé leur importance au plus fort de la crise sanitaire en Chine, vu le niveau de saturation des hôpitaux.
La création des pièces en cuivre en utilisant les méthodes de production classique n’est pas aisée. Pourtant, grâce à la fabrication additive, une telle opération s’apparente à un jeu d’enfants. En plus de la rapidité et de l’économie offertes par cette alternative, l’efficacité du cuivre contre les bactéries, les virus et les champignons pathogènes est scientifiquement prouvée.
L’on estime, aujourd’hui, à 96 % la capacité d’élimination des virus du Covid-19 par le cuivre. C’est probablement ce qui justifie la modification initiée par SPEE 3D sur ses imprimantes. Cette entreprise australienne a en effet développé de nouveaux algorithmes permettant de recouvrir de cuivre les pièces métalliques afin d’empêcher la propagation de la maladie.
Production d’équipements de protection individuelle
La pénurie en équipements de protection individuelle a été durement ressentie par le secteur médical aux premières heures de la crise sanitaire. Il en est ainsi des visières de protection, des masques de protection respiratoire et d’autres équipements du même type qui ont cruellement fait défaut au milieu de la première vague épidémique.
L’aide apportée par la technologie d’impression 3D a été très précieuse. En fournissant des logiciels open source, Prusa a permis à tous les détenteurs d’imprimantes 3D de produire massivement des visières de protection. Un grand nombre d’entreprises spécialisées en ont profité pour se lancer dans la production à grande échelle des EPI.
L’utilisation des masques de protection respiratoire s’est répandue avec l’apparition de la pandémie. Malgré son caractère obligatoire, le port du masque n’empêche pas la pluralité des modèles disponibles sur le commerce. Or, certains d’entre eux présentent quelques imperfections capables de créer des nuisances et d’en réduire l’efficacité.
L’impression de fibres sensorielles 3D est l’une des solutions proposées pour résoudre le problème. Cela consiste à insérer des dispositifs de très petite taille semblables à des capteurs. Leur rôle est de détecter les failles à travers le souffle ou le mouvement des cellules. La création de ces fibres sensorielles se fait grâce à l’argent et aux polymères imprimés en 3D qui agissent comme des semi-conducteurs.
Participer à la conversation